二酸化炭素の削減に向け、木材パルプを原料とする新素材「セルロースナノファイバー」が注目されている。プラスチックと混ぜた合成樹脂は軽量で強度があり、車の部品に使えば燃費が向上し二酸化炭素の排出を抑制できる。ただ、今は製造コストが高く、量産化に向けた研究が続いている。
環境にやさしい新素材
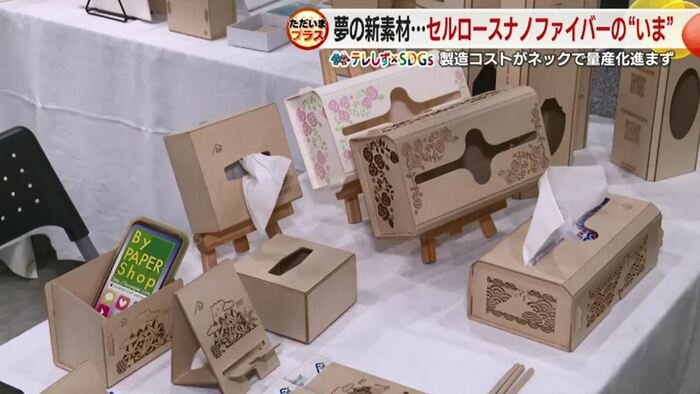
2024年10月に静岡県富士市で開かれた展示会。
並んでいたのはいずれもセルロース素材を使った製品で、企業や大学など約120の団体が参加した。
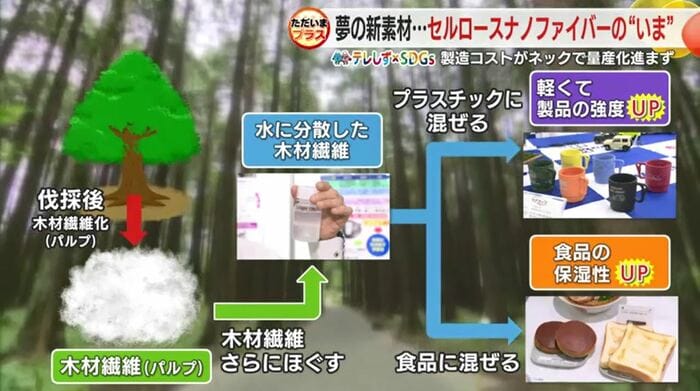
セルロース素材は木材パルプを原料とする繊維で環境にやさしい。
プラスチックなどに混ぜて使うことで軽くて強度が高い製品ができるほか、食品に混ぜることで保湿性が増すことで知られている。
木から作られた未来の車
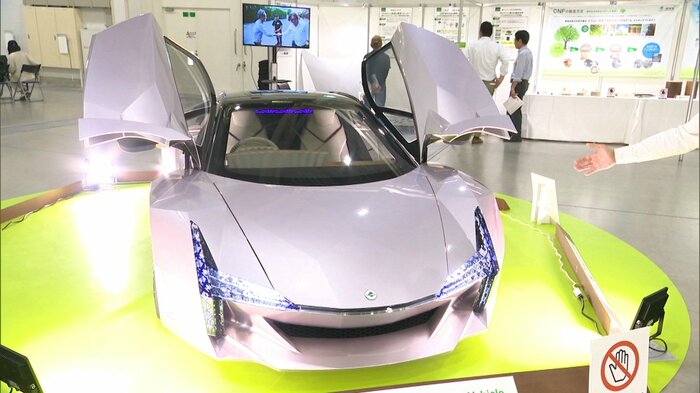
中でも期待されているのが自動車産業におけるセルロースナノファイバーの実用化だ。
展示会には環境省や自動車メーカーなどが連携して作った試作品として、”未来の車”が展示された。
ボンネットやドアパネル、窓ガラスの素材としてセルロースナノファイバーが使われていて、強度を増した上で車体の軽量化を実現。
これにより燃費が向上し、二酸化炭素の排出削減につながる、まさに”未来の車”だ。
強度を増すには難しい技術が必要
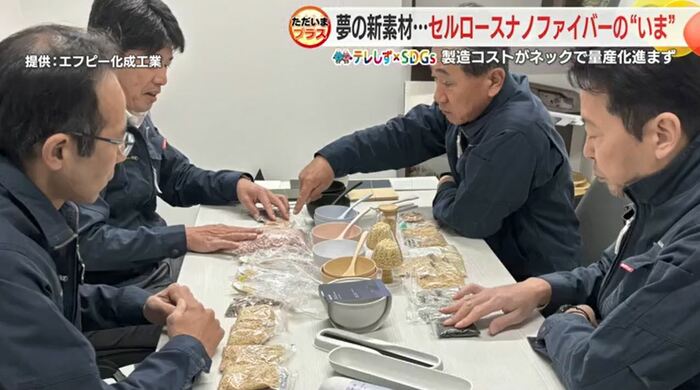
富士市にあるプラスチックの原料を作る合成樹脂メーカー・エフピー化成工業。
近年、セルロースナノファイバーを使った合成樹脂の開発や製造に注力している。
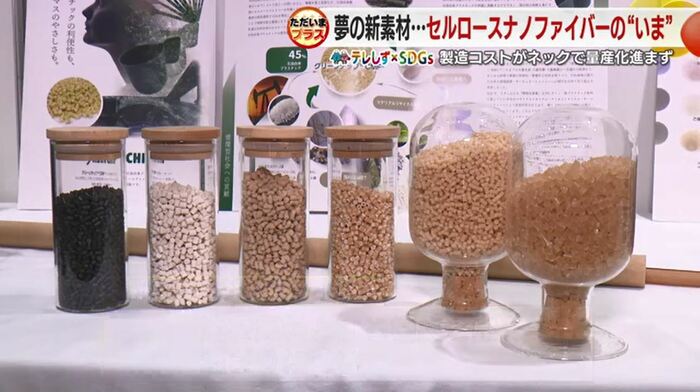
エフピー化成工業・赤澤英郎 社長:
我々は木材由来のセルロース繊維をプラスチックに配合している。細かくしたセルロースを「ポリプロピレン」というプラスチックの中に練り込む。セルロースを均一に樹脂の中に分散させることで強度のある樹脂を作るが、(セルロースを均一に)分散させるのは非常に難しい技術と言われている
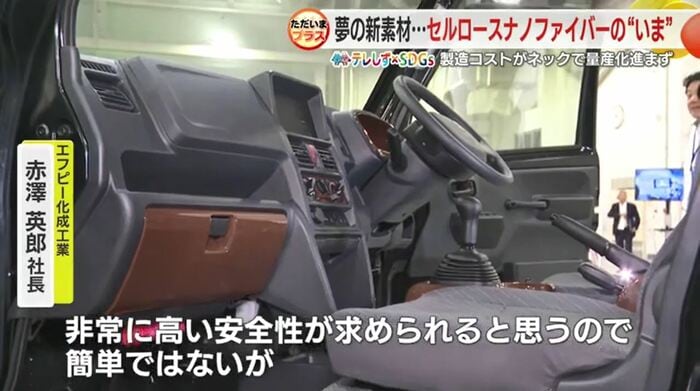
一般にセルロースナノファイバーは油を原料とする樹脂とは混ざりにくいと言われていて、各社が開発にしのぎを削る中、エフピー化成工業では7年以上の歳月をかけて独自の製法で合成樹脂を作り出すことに成功。
他の企業と連携しながら製品化に向けた取り組みを進めていて、今回の展示会でも自動車メーカーがエフピー化成工業の合成樹脂を使って作ったバンパーグリルや内装品を採用した自動車が紹介された。
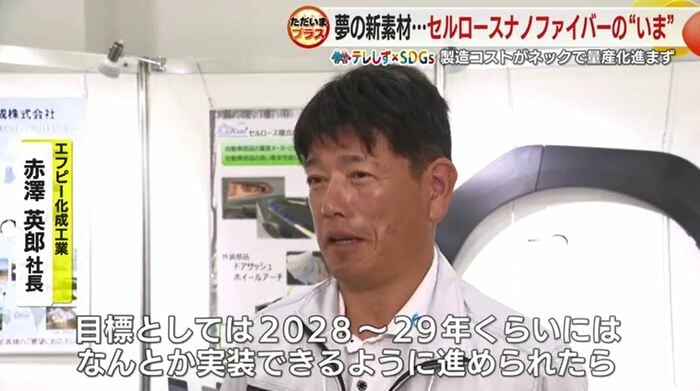
エフピー化成工業・赤澤英郎 社長:
非常に高い安全性が求められると思うので簡単ではないが、目標としては2028~29年くらいにはなんとか実装できるように進められたら
量産化に向け新装置を開発中
SDGsの重要性が叫ばれる現代にあって、セルロースナノファイバーはカーボンニュートラルに貢献する、まさに“夢の素材”だ。
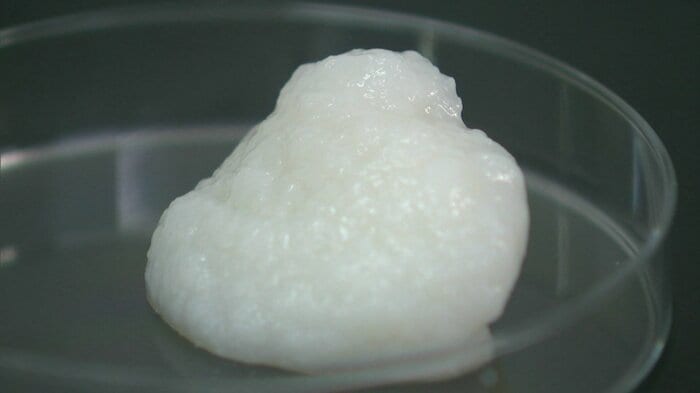
ただ、一方で課題もある。
静岡県工業技術研究所CNF科・山下晶平 科長:
企業が第一に言うのが製造コスト。植物から取り出すセルロースだが、ファイバーに細かくしていく上でエネルギーのコストが非常に無視できない
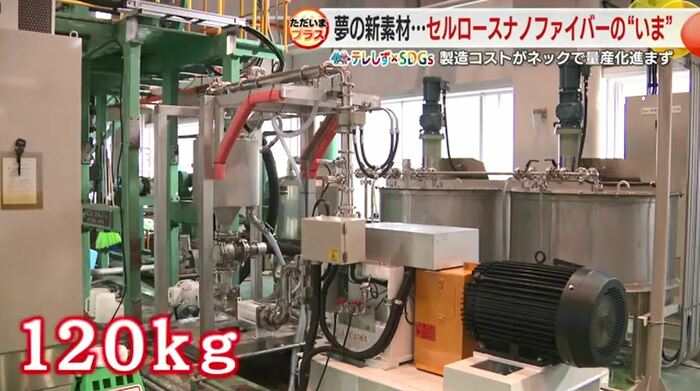
製造コストがネックとなり量産化が進んでおらず、このため、静岡県工業技術研究所の山下さんは民間企業と連携して、1日に数十グラムしか作れなかったセルロースナノファイバーを、これまでとは比べ物にならない120キロまで製造できる装置を開発。
コストダウンにつなげられるよう、日々 研究に奮闘している。
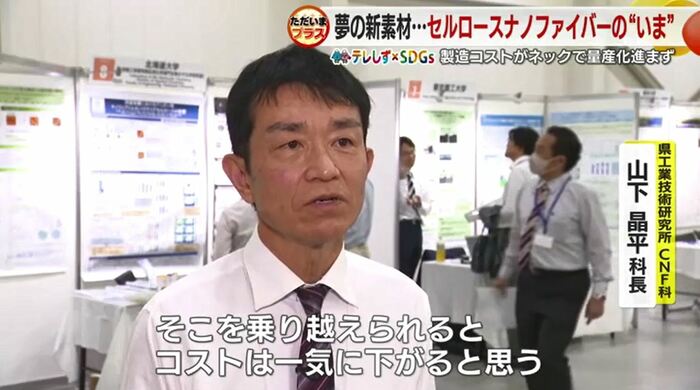
静岡県工業技術研究所・山下晶平 科長:
(量産化に向け)まだ試作品開発の段階という部分がけっこうある。なかなか大量生産というところまでこぎつけていない状況。そこを乗り越えられるとコストは一気に下がると思う
セルロースナノファイバーをめぐっては、県が製品開発の支援・研究開発の強化・製造拠点の形成を三本柱としていて、今後どのような発展を遂げるのか注目される。
(テレビ静岡)